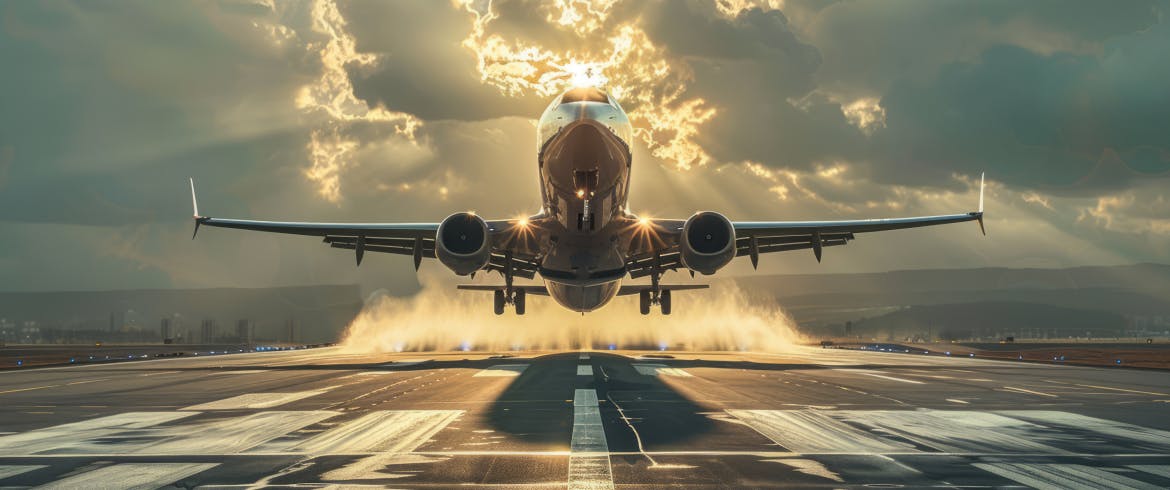
Supply Chain Improvement Strategy Roadmap
This article outlines a multi-phased approach to maturing your supply chain. This structured roadmap provides a clear path for improvement, enabling you to optimize inventory, increase supply chain efficiency, and ultimately drive significant cost savings.
The Journey: This roadmap outlines the essential stages of maturity, highlighting that effective processes evolve over time and that there are no shortcuts to achieving excellence. SkySelect is your trusted partner on this journey, offering the expertise, technology, and guidance needed to navigate each phase effectively.
Key Principles:
- Process-Focused: We begin with a foundational approach and gradually evolve towards more sophisticated, data-driven strategies.
- Long-Term Vision: This roadmap is a strategic blueprint for the remainder of the year and beyond, ensuring continuous improvement and sustained success.
- Incremental Gains: With each step, you'll observe tangible improvements in supply chain efficiency, inventory optimization, and overall operational performance.
Supply Chain Maturity Steps
PHASE 1 — Manual Quoting: Quotes are usually received manually, either by phone or through email.
PHASE 2 — Contract: Parts are placed under contract primarily to enhance efficiency and negotiate reasonable prices. This is typically done for fast-moving or single-source parts.
PHASE 3
Automated Sourcing Driven by Data: Automate the multi-round sourcing process according to your business rules. Capture savings and improvements in lead time. Monitor availability and identify new sources—automate purchase order decisions for lower-cost parts, with potential savings of around 95%.
Automated Order Management Driven by Data: Streamline transmission, follow-up, and tracking processes. Enhance decision-making and change management. Utilize supplier scorecards for continuous improvement. Provide real-time EDD updates based on established standards and historical performance.
PHASE 4 — Segmented Supply Chain Management:
Define an effective strategy at the part level, utilizing analytics. Typically, contracts are established for high-risk and single-source parts. For medium- to low-risk parts, source from a diverse range of suppliers in the broader market. Automate PO decision-making based on viability and EDD. Regularly review the supply chain strategy to adapt to changing market conditions.
PHASE 5 — TCO Optimization Powered By Data:
A comprehensive cost model encompasses purchase, logistics, warehousing, and emergency costs. The supply chain strategy is dynamic, with decisions optimized to achieve the minimum Total Cost of Ownership (TCO) at the individual part level instead of at the category level.
Inventory Maturity Steps
PHASE 1 — Purchase on Request: Implement a basic purchase-on-request system to address immediate demand.
PHASE 2 — MIN-MAX: Implement a MIN-MAX inventory control system to maintain optimal stock levels, particularly for fast-moving items.
PHASE 3
Real-Time Data-Driven Planning: Utilize real-time data to guide inventory planning decisions and optimize stock levels. The PN inventory strategy will be informed by current market conditions.
Inventory Balancing: Surplus and inventory are shared on SkySelect and balanced across regions or within the business units of the same company. SkySelect can be used to facilitate transactions.
PHASE 4
Collaborative Forecasting: Collaborate with suppliers to enhance forecast accuracy and reduce demand variability. Share monthly demand and usage data with suppliers. Agree upon joint supply chain plans and address potential supply chain risks. Align these efforts with consignment agreements.
Virtual Pooling: Pooling amongst customers of strategic inventory. This involves sharing strategic inventory and implementing processes to enable the sharing.
PHASE 5 — Inventory Pooling: Explore innovative inventory pooling models to optimize stock levels and reduce inventory costs. PNs are consolidated at a central location, allowing safety stock to be pooled and replenished from this central site. This process is managed by a third party, guided by demand and supply plans.
Getting Started
To kick-start this transformative journey, we will conduct a comprehensive Supply Chain Strategy Workshop. This collaborative session will focus on:
- Defining Scope: Clearly outline the specific focus areas for your supply chain improvement initiative.
- Developing an Analytical Model (TCO): Establishing a robust framework for evaluating the total cost of ownership across your supply chain.
- Identifying Potential Solutions: Exploring innovative solutions tailored to your unique business needs and challenges to ensure you feel understood and catered to.
Driving Supply Chain Excellence with SkySelect
SkySelect's technology platform is designed to support your organization at every stage of the supply chain maturity journey. Key features and capabilities include:
- Data-Driven Insights: Access real-time data and advanced analytics to gain deep insights into your supply chain performance.
- Automated Sourcing: Streamlined sourcing processes, including automated RFQs, supplier evaluations, and contract negotiations.
- Inventory Optimization Tools: Powerful tools for inventory forecasting, planning, and optimization, including demand forecasting, safety stock calculations, and what-if analysis.
- Supplier Collaboration: Enhanced supplier collaboration through secure communication channels, shared data, and joint planning initiatives.
- Continuous Improvement: Ongoing monitoring and analysis of supply chain performance to identify areas for improvement and drive continuous optimization, ensuring your supply chain is constantly evolving.
Benefits of Partnering with SkySelect:
- Accelerated Time-to-Value: Rapidly implement supply chain improvements and achieve tangible results within a shorter timeframe.
- Reduced Costs: Significant cost savings through optimized sourcing, reduced inventory holding costs, and improved operational efficiency.
- Increased Agility: Enhanced agility and responsiveness to market changes and unforeseen disruptions.
- Competitive Advantage: Gain a competitive edge by building a more efficient, resilient, and cost-effective supply chain.
Conclusion
SkySelect's aircraft parts procurement technology empowers you to navigate each step of this roadmap successfully. Our team, with extensive experience and expertise, will guide you through every phase of this process, providing comprehensive insights to optimize your supply chain. This will drive significant cost savings while enhancing your organization's agility, resilience, and overall success. By embracing this strategic roadmap and leveraging SkySelect's technology, you can transform your supply chain into a competitive advantage.
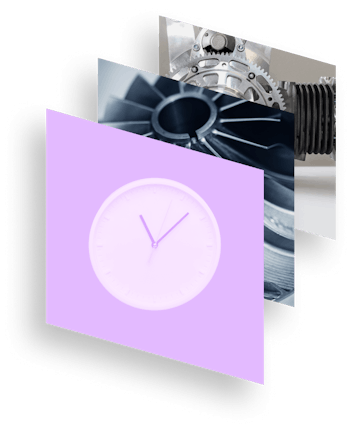
Contact SkySelect to learn more about our supply chain improvement solutions and how we can help you achieve your business goals.