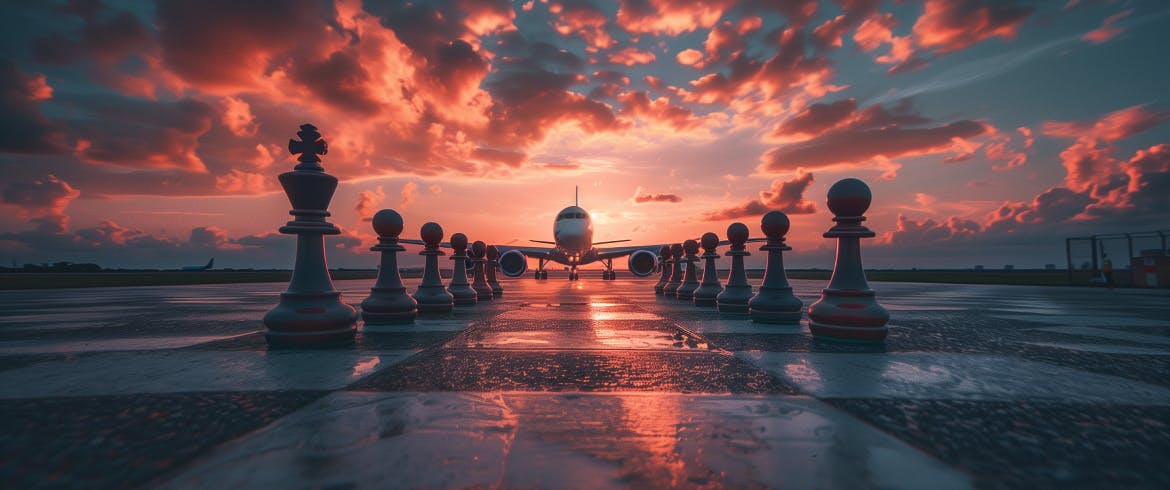
How Turnaround Management Can be Utilized to Improve the Parts Procurement Process
By Tulika Dayal
Times are tough in the aviation supply chain. Travel demand is projected to surpass pre-pandemic levels, but due to production challenges at OEMs, aircraft deliveries are dropping sharply. This means airlines are challenged with trying to satisfy summer travel with less planes and a shrinking supply of parts and materials.
Rising costs and increasing obstacles are piling up for the procurement departments of airlines and MROs. So what might be the remedy to alleviate the pressure of these challenging times? Turnaround management.
What is Turnaround Management?
Turnaround management is the process of transforming a faltering department or organization into a profitable or more efficient operation by reorganizing its leadership, processes, and finances.
Turnaround management is an agile, structured approach to a situation that, if untreated, could lead to catastrophic consequences.
While turnaround management involves financial decisions such as cutting costs, it also aims to solve a multitude of issues such as stagnation and procedural inefficiencies in a company’s business model, leadership or culture.
After the problem is addressed, a new strategy or process can be implemented to put the company back on a growth trajectory.
What’s important to understand about turnaround management is that a company doesn’t have to be in crisis or dire straits to implement turnaround strategies. As a matter of fact, it can be more useful and effective if turnaround management can be implemented before the situation becomes critical.
Alternatively, organizations that are simply maintaining the status quo or ones that need to make changes to current operating models can benefit from turnaround management.
Turnaround Management Applied to Procurement
Now that we established a baseline understanding of turnaround management, let’s examine how it can be applied to aircraft parts procurement.
As outlined in the introduction, the current aviation supply chain has created a very challenging procurement environment. Not only is the supply of aircraft and aircraft parts low, this summer’s anticipated demand, although a welcome sign for industry, is expected to really test the fortitude of aviation organizations.
Even the strongest and healthiest airlines will be put to the test. Purchasing teams are under increasing pressure as they attempt to procure parts while facing rising costs, long lead times, and working around a resource crunch.
It’s clear that old tools and old processes can no longer cope with the variables that airlines are confronted with in this new age of aviation, which sets the stage for turnaround management to act as a necessary catalyst of change.
Specifically, turnaround management can be deployed to improve two components that go hand-in-hand — strategic focus and critical processes.
Purchasing teams have always been tasked with balancing its workforce with market demands. Even during more typical demand patterns, it can be challenging to strike the right balance.
Then we experienced extreme versions of these ebbs and flows during and after the peak of the pandemic. Airlines were forced to cut large portions of their staff when travel came to an abrupt halt, while other employees left on their own seek presumably greener pastures in a new industry.
This has created a severe labor shortage, specifically in skilled areas such as parts sourcing and procurement which have significant impacts on operational performance, making it clear that a different strategy and new processes must be implemented.
The best turnaround strategy for this particular problem is digital transformation through technological adoption. Specifically, AI can assist purchasing teams and increase productivity by automating many day-to-day tasks and processes by leveraging structured data.
By using procurement AI technology, airlines and MROs can reduce the manual effort of their procurement teams by up to 90%.
It is much easier to scale up and down with technology as opposed to constantly managing to have the right amount of employees on staff. It’s much easier and less costly to hit pause on a piece of software than it is to make personnel adjustments.
Procurement AI can simultaneously manage hundreds of requests in minutes instead of days or weeks. When experiencing downtime, money doesn’t need to be spent on resources not being used. You pay a small percentage fee on each transaction executed by your technology platform.
This frees up purchasing teams to focus their attention where human ingenuity is needed for more strategic tasks.
And not only does automating processes with AI help address output, it also improves it tenfold. On average procurement teams experience a 20% reduction in costs, a 15% increase in on-time performance and 100 times faster cycles from the time of part requirement to a PO.
Deploying AI technology with a proper change management plan is the fastest and most effective way to execute turnaround management of a purchasing team, and frankly, is critical to future success and scalability. A proper deployment quickly and significantly enhances the strategic focus and improves outdated processes.
Times are changing, so your organization must also change. Don’t wait any longer!